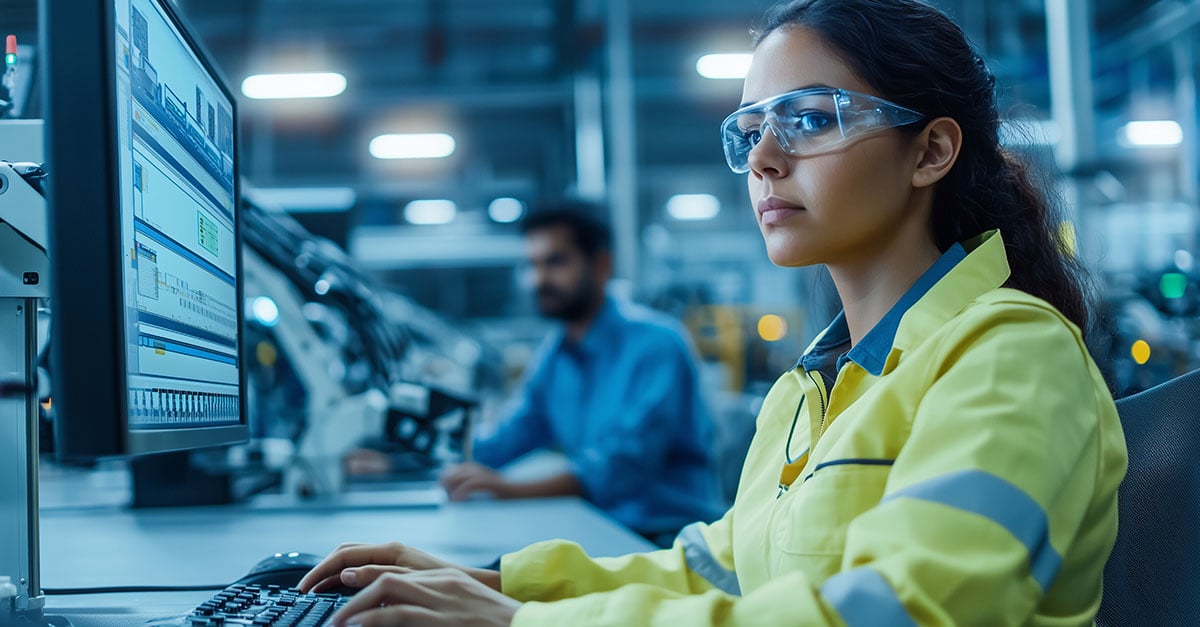
La digitalizzazione di fabbrica oltre "Industria 4.0"

Le soluzioni realizzate per i requisiti 'Industria 4.0' sono spesso limitate nel supportare una completa digitalizzazione di fabbrica.
Scopri come superare i limiti delle interconnessioni 'base' realizzate per rispondere ai requisiti del Piano Nazionale Industria 4.0, ed ottenere soluzioni scalabili, modulari e interoperabili, per supportare la trasformazione digitale della fabbrica.
L’importanza di soluzioni scalabili
Un pilastro in ogni programma di digitalizzazione industriale è l'interconnessione estesa dei macchinari di produzione, con i sistemi di gestione della produzione (ERP, MES, schedulatori) ma potenzialmente con molti altri, garantendo lo scambio bidirezionale di dati in tempo reale.
Questo flusso informativo comprende:
- Dati di funzionamento della macchina: (stato, allarmi) monitoraggio continuo per prevenire fermi imprevisti
- Dati di produzione: quantità programmate e prodotte, scarti, tempi ciclo
- Istruzioni operative: ricette di processo, setpoint e programmi di lavorazione
L’obiettivo è consentire il monitoraggio continuo e l’analisi in tempo reale di macchine e processi, riducendo:
- fermi macchina non pianificati
- gli scarti di produzione
- i tempi di inattività
Incentivi e criticità attuali
Il Piano Nazionale Industria 4.0 ha sostenuto questa necessità con incentivi fiscali per chi acquistava 'beni strumentali interconnessi con il sistema gestionale di fabbrica'. Purtroppo, in molte aziende, l'interconnessione è stata realizzata in modo minimale, finalizzata più che altro a 'spuntare' i requisiti di legge ed ottenere un beneficio fiscale immediato. Sono stati rari i progetti di digitalizzazione sostenibile nel lungo periodo, aperti a future evoluzioni.
Queste soluzioni essenziali si dimostrano ora insufficienti per:
- Scalare la digitalizzazione e nuovi reparti o linee di produzione
- Adottare tecnologie di manutenzione predittiva e condition monitoring
- Integrare facilmente nuovi macchinari o protocolli di comunicazione
- Implementare soluzioni di cybersecurity
Perché superare i limiti delle interconnessioni 'base'
Collegare macchine e sistemi gestionali (ERP, MES, SCADA) con soluzioni 'base' può bastare per ottenere gli incentivi fiscali, ma presenta tre problemi chiave:
- Requisiti minimi: le implementazioni essenziali servono solo a "spuntare" i vincoli di legge, senza offrire reale valore operativo
- Colli di bottiglia: con l'aumentare delle esigenze(più dati, protocolli diversi, reporting avanzato) emergono criticità che frenano l'evoluzione dell'impianto.
- Costi e rigidità: ogni upgrade diventa complesso e oneroso, perché l'architettura non è pensata per essere flessibile e modulare.
Per avviare una vera trasformazione digitale, è quindi fondamentale superare queste soluzioni di base e adottare piattaforme progettate per integrare, scalare e innovare con pochi sforzi aggiuntivi.
Le 4 criticità della digitalizzazione di fabbrica
Nel percorso verso la realizzazione di una smart factory, emergono 4 "colli di bottiglia" che rallentano la scalabilità e l'interconnessione dei macchinari.
- Sistemi che supportano solo protocolli moderni
- Integrazioni "custom" poco espandibili
- Introduzione di nuovi sistemi di analisi dati
- Cybersecurity
1. Sistemi realizzati che supportano solo protocolli moderni
Molte piattaforme gestionali si integrano nativamente con macchine di ultima generazione tramite OPC-UA o MTConnect, ma spesso non riconoscono protocolli legacy presenti in tantissime macchine (vedi anche: La sfida della connettività: i sistemi legacy).
Questo era sufficiente per l'interconnessione dei nuovi macchinari incentivati. Quando però si presenta la necessità di interconnettere macchinari più datati (e magari altrettanto strategici all'interno di un progetto di monitoraggio di processi produttivi), queste soluzioni non sono in grado di dialogare facilmente con i numerosi protocolli 'legacy' dei macchinari.
Conseguenza: la complessità e i costi di implementazione salgono vertiginosamente, arrivando al paradosso che interconnettere una macchina “vecchia” può costare molto più che per una macchina nuova.
2. Integrazioni “custom” e poco espandibili
Nel secondo scenario, per realizzare l’interconnessione (e rispettare i requisiti di legge) si è scelto di realizzare integrazioni estremamente basilari, spesso basate su:
- Scambio di file CSV o database ‘ponte’ con poche variabili (contapezzi, stato macchina, allarmi essenziali)
- Sviluppi ad hoc o script interni che leggono e scrivono dati tra macchine e applicazioni
Questi metodi funzionano per trasmettere le poche informazioni richieste per attestare l’interconnessione '4.0', ma quando l’azienda vuole estendere la raccolta dati (ad esempio per manutenzione predittiva, controllo dei consumi, o per supportare i requisiti di “Industria 5.0”), le soluzioni 'base' si dimostrano inadeguate.
Aggiornarla diventa rischioso (si teme di impattare sul sistema esistente) e costoso, sia per i tempi di sviluppo sia per la mancanza di un’architettura progettata per gestire nuovi use case.
Case study: manutenzione predittiva in Industria 4.0
3. Introduzione di nuovi sistemi di analisi dati
Un’evoluzione particolarmente frequente si verifica quando l’azienda desidera introdurre un nuovo sistema di reporting o di analisi dati in affiancamento al sistema gestionale, che necessita di:
- Quantità di informazioni più elevata (es. decine o centinaia di variabili per macchina)
- Campionamenti dati più frequenti
- Tipologie di dati differenti (non solo contapezzi e stato macchina, ma anche log dettagliati, parametri di funzionamento macchina, parametri di consumo, ecc.)
Se l’interconnessione esistente è nata per scambiare solo poche variabili e con modalità quasi-batch (file CSV o mini-DB di scambio), integrare queste nuove esigenze può risultare praticamente impossibile senza rifare tutto da zero.
Anche qui, i costi e i tempi di reingegnerizzazione lievitano, ed il rischio di creare ulteriore complessità o di impattare il sistema produttivo in funzione rende il progetto poco sostenibile.
4. Cybersecurity
Molte integrazioni 'base' sono state realizzate avendo un'attenzione ridotta ai requisiti di cybersecurity, ad esempio usando numerose cartelle di scambio dati/files, utilizzo di comuncazioni non criptate tra gestionale e macchine, scarsa separazione architetturale tra 'OT' e 'IT'. Mitigata dal fatto di interconnettere macchine più moderne, con sistemi operativi più aggiornati e securizzati.
L'ampliamento della superficie di attacco determinata dalla necessità di espansione dell'interconessione di altre macchine, anche più datate, e magari dotate di sistemi di controllo basati su OS fuori supporto (es. Windows XP) richiede un ripensamento architetturale anche rispetto alle necessità impellenti di garantire un livello minino di sicurezza informatica, anche in ottica di compliance con le direttive NIS2.
digitale della tua azienda con Alleantia Core
Perché serve una “Release 2” dell’Industria 4.0.
Le criticità riscontrate nelle implementazioni iniziali impongono di ripensare la strategia di digitalizzazione e valutare seriamente una "IoT Release 2" a supporto delle soluzioni Industria 4.0 e delle loro evoluzioni per una digitalizzazione estesa della fabbrica.
Questo implica:
- Sostituzione delle integrazioni obsolete: elimina soluzioni ad hoc e CSV-batch, passando a gateway IIoT certificati.
- Integrare nuove piattaforme ingegnerizzate in affiancamento al sistema esistente, così da ridurre i rischi di fermi e semplificare l'evoluzione verso una architettura consolidata con funzionalità avanzate.
L' obiettivo della 'IoT Release 2' è di supportare i requisiti di digitalizzazione complessivi dell'azienda, funzionali all'efficienza produttiva, ottimizzazione costi e riduzione fermi, disponendo di un'architettura modulare, flessibile e scalabile, capace di:
-
Integrare qualsiasi tipo di macchinario (nuovo o datato) con diversi sistemi applicativi.
-
Garantire l’accesso a più variabili e parametri di macchina in modo incrementale e modulare, senza dover riprogettare l’intero sistema.
-
Ridurre i costi e i tempi di implementazione, evitando gli sviluppi custom che rallentano l’innovazione.
-
Interconnettere facilmente più applicativi e piattaforme, anche in cloud.
- Supportare requisiti aumentati di cybersecurity
Per una vera evoluzione delle soluzioni Industria 4.0, è quindi indispensabile:
- Interoperabilità: collegare ogni macchina (nuova o legacy) con diversi sistemi applicativi.
- Modularità: aggiungere macchine e variabili senza riscrivere il codice.
- Scalabilità: far crescere l’infrastruttura gradualmente, senza blocchi produttivi.
- Costi contenuti: ridurre tempi di progetto ed evitare sviluppi custom.
Alleantia Core: la soluzione “buy” per la “IoT Release 2”
Quando si parla di soluzioni di interconnessione “ready-to-use”, uno dei prodotti leader sul mercato è Alleantia Core, utilizzato in moltissime realtà industriali. Grazie a una piattaforma ingegnerizzata e consolidata, Alleantia Core elimina le complessità tipiche dei progetti “fai da te” e permette di colmare le lacune delle tre situazioni problematiche descritte.
Alleantia Core è una piattaforma “ready-to-use” ideale per superare i 4 scenari problematici:
- Connessione pronta per migliaia di tipologie di macchine, anche di più di 20 anni di età.
- Supporto a oltre 20 protocolli di interconnessione di applicazioni (OPC-UA, MQTT, SQL, REST e legacy).
- Architettura modulare e configurabile: nessun codice personalizzato per estendere o migrare.
- Elevata sicurezza informatica grazie a comunicazione criptata, configurazioni criptate, architettura distribuita.
- Affidabilità industriale: migrazione “a passi” senza impatti sul sistema in produzione.
- Modello di abbonamento annuale: investimento diluito in base al numero di macchine connesse.
Caratteristica | Interconnessione Base | Alleantia Core |
---|---|---|
Interconnessione | Batch (CSV/database ponte) | Real-time |
Protocolli Supportati | 1–2 (proprietario, OPC-UA/MTConnect per nuove macchine) | +20 (OPC-UA, MQTT, SQL, REST, Modbus, Profibus, ecc.) |
Architettura | Custom, point-to-point | Modulare, gateway IIoT distribuiti |
Configurabilità | Script/manuale, ogni modifica richiede sviluppo | Drag-&-drop di variabili e macchine, nessuna riga di codice |
Scalabilità | Rigidità su volumi e nuovi use case | Espansione “step by step” per reparti, linee e siti multipli |
Affidabilità | Rischio di downtime per upgrade | Migrazione parallela, zero impatto sul processo produttivo |
Manutenzione Predittiva | Impossibile o molto complessa | Nativamente supportata, con accesso a centinaia di variabili in real-time |
Time-to-Value | 3–6+ mesi per ogni estensione | Pochi giorni/settimane per nuovi moduli |
Modello di spesa | Capex elevato per ogni sviluppo | Opex: abbonamento annuale per macchina connessa |
ROI | Lungo e incerto | Accelerato, grazie a costi diluiti e rapido deployment |
Integrazione gestionale | Spesso richiede personalizzazioni dell’ERP/MES | Plug-&-play con traduzione protocolli, senza modifiche al gestionale |
Conclusioni
Alleantia Core rappresenta una risposta concreta: grazie al suo vasto supporto di protocolli e API, alla facilità di integrazione e alla affidabilità dimostrata in numerose realtà industriali, permette di abilitare o migliorare l’interconnessione di qualsiasi macchina, vecchia o nuova, e di espandere la digitalizzazione verso nuovi orizzonti come manutenzione predittiva, condition monitoring e controllo dei consumi per l’Industria 5.0. Il modello ad abbonamento permette poi una diluizione dei costi nel tempo, senza richiedere importanti investimenti una tantum.
Se la vostra azienda sta valutando una “Release 2” delle vostre soluzioni Industria 4.0, o se state incontrando problemi nello scalare i progetti di digitalizzazione, vi invitiamo a contattare gli esperti di Alleantia per una consulenza su misura per la valutazione delle vostre esigenze.
Grazie alla modularità e alla potenza di Alleantia Core, potrete realizzare un nuovo passo avanti nel vostro programma di trasformazione digitale, in modo efficace ed economicamente sostenibile.