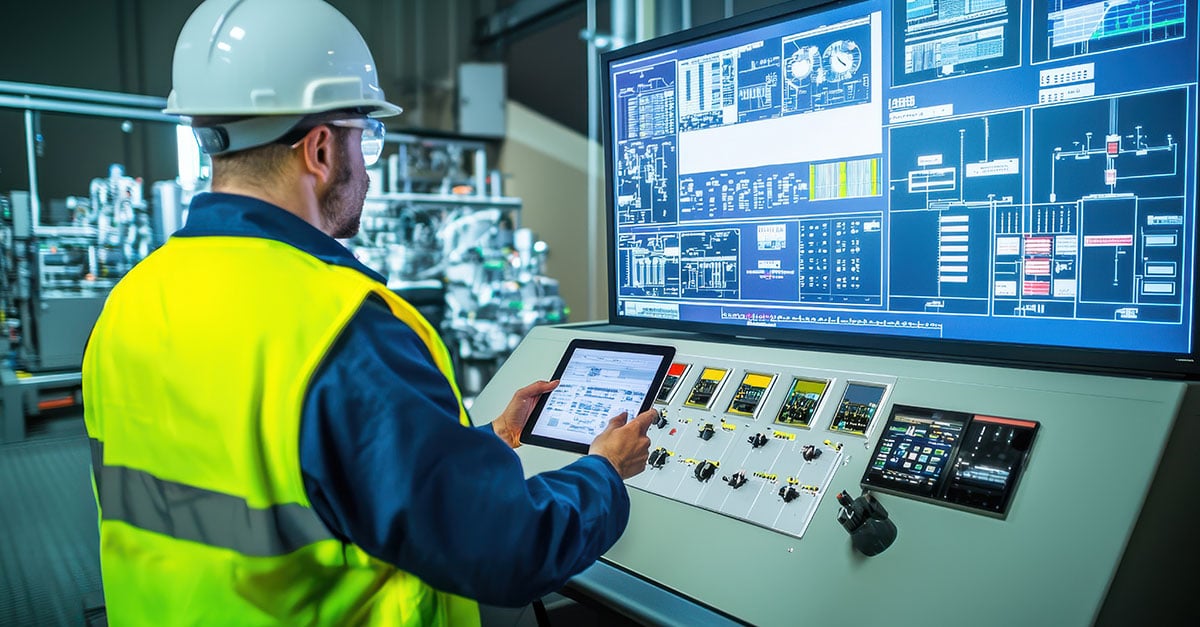
A multiplatform strategy. The value of interoperability in Industry 4.0.

In the context of industrial digitalization and Industry 4.0, a multiplatform strategy based on interoperability and machine connectivity is the key to overcoming information silos and maximizing data value, for immediate and future benefits.
INTRODUCTION
In the rapidly changing world of industrial manufacturing, digital transformation has become an imperative. From small manufacturers to global companies, all are striving to optimize and transform production and maintenance processes using data from machines, production lines, meters, sensors, etc.
Why? Because real-time machine information is extremely useful in understanding how to increase productivity, improve product quality, reduce waste, and reduce operating costs.
Implementing industrial digitization with a strategis approach, rather than acquiring, orchestrating and analyzing machine data in vertical 'once for all model' it means ensuring that the designed solution will be capable to support a wide range of platforms, current and future, and will avoid the creation of 'data silos' that later will become obstacles to the necessary evolution of the enterprise and of its digitization.
Learn how an open, future-proof architecture, capable of integrating PLCs, MES, ERP, and cloud solutions such as AWS, Azure, Splunk Cumulocity and SAS , accelerates processes, facilitate OEE improvement, reduces integration costs and enable creation of many 'digital factory applications'.
In this article, we will explore the main advantages of a platform that support legacy protocols, modern protcols like REST API and MQTT and certified connectors for specialized cloud platforms, allowing ICT managers to freely choose the most innovative technologies for your connected factory.
Why is interoperability the real driver of the Digital Industry?
In an increasingly connected and dynamic manufacturing environment, breaking down information silos and adopting open architectures makes all the difference.
The 'infographic below summarizes the key benefits, from revenue growth to waste reduction to time savings per employee, that companies achieve by integrating systems, data, and platforms in a seamless, cross-platform way.
maximum operational
(From Accenture Research) AccentureAccenture
Interpretation
-
Accelerating growth: a high level of interoperability unlocks value beyond simple technical integration, multiplying revenue growth.
-
Increased agility: working on open, interoperable platforms not only reduces integration costs, but frees up valuable time (about two hours per day per employee) → more focus on innovation and competitiveness.
-
End-to-end efficiency: benefits reverberate throughout the entire value chain (supply chain, operations, customer experience, HR management and sustainability), confirming that cross-platform architectures are the basis for truly “future-proof” digital transformation.
These data demonstrate unequivocally that investing in interoperability is not just an IT best practice, but a strategic driver of growth, efficiency, and resilience.
Below, you will find key considerations for anyone with an interest in the industry, for business decision makers responsible for making technology investment choices, for ICT managers, and for production and operations managers.
We will explore the ‘importance of a versatile and 'future-proof’ architecture, and illustrate how solutions such as Alleantia Core software accelerate the digital transformation, while still keeping options open to manage future evolutions, and thus current and future integration costs and time needed.
The age of machine data
Modern production lines can generate gigabytes of data every day, from sensor readings and machine logs to operational metrics, enterprise resource planning (ERP), and manufacturing process management (MES).
Level | Period | Data volume | Equivalence in GB/day |
---|---|---|---|
Production Line | 1 giorno | > 1.4 TB | > 1.400 GB |
Smart factory | 1 week | ≈ 276 TB | ≈ 55.000 GB |
Single machine | 1 week | ≈ 345 GB | ≈ 69 GB |
(Illustrative, based on real implementation)
The next critical step is to convert this data into usable information. In particular, by consistently using 'on edge' solution to consolidate data volumes, extracting the most relevant information. However, many organizations fall prey to “vertical silo” deployments, where data is then locked into a single platform or application. This is mainly due to haste, little time to define, design and select solutions with open architectures, often following an opportunistic 'quick hit' approach and use/extension of known solutions, perhaps alredy present in the company.
Avoid data silos
A successful 'digital transformation initiative' should ensure that machine data remain easily usable for new applications, data analytics platforms, data science and self-learning tools that are already available and others that will emerge in the future.
This is critical because an initial “high priority” project, such as integrating production data into ERP. It will almost certainly be followed by subsequent initiatives on 'data analytics, artificial intelligence-based decision making, or specialized solutions to support the shopfloor in improving its operations.
'Future proofing' requires open architectures
When you rely on closed, proprietary systems, you risk high integration costs, challenging migrations, and often the need for specialized expertise in the future.
An open architecture that provides standardized machine data models, combined with ready-to-use integration capabilities, can greatly reduce the time-to-market for new use cases.
It also allows experimental projects (PoCs) to be implemented more easily, enabling organizations to test new platforms and solutions with minimal effort and expense.
1. Multiplatform as an enabling scenario
- Definition: a cross-platform solution natively supports different protocols, formats and environments (PLC, SCADA, MES, ERP, AWS/Azure cloud, MQTT, SQL, noSQL, REST, mobile, etc.).
- Advantage: eliminates technological constraints that create “silos” and limits to integrations.
2. Interoperability as a key capability
- Definition: interoperability is the ability to make heterogeneous systems “talk” to each other, exchanging data consistently and without loss of context or semantics.
- Advantage: ensures that machine, process and business data can flow freely between platforms, avoiding redundancy, duplication and costly customization.
3. The natural link
Multiplatform | Interoperability |
---|---|
Provides APIs, connectors and SDKs** to connect different technologies “out-of-the-box” | Adopt standard data models (e.g., OPC UA, MQTT, REST) to make different parts talk to each other |
Supports fieldbus, legacy and modern cloud protocols without custom build-ins | Converts data to interoperable formats, reducing integration time and cost |
Allows a choice of multiple vendors (edge, analytics, AI) depending on use cases | Ensures that new tools and platforms can be integrated without rewriting the architecture |
How to realize a scalable and open digital industry platform?
1. Multiplatform connectivity
- The IoT solution you choose must natively support a wide range of industrial communication protocols and data exchange formats.
This includes classic fieldbuses, proprietary machine interfaces, modern protocols such as MQTT, REST APIs for Web applications, and direct integration with popular databases and cloud environments.
2. Scalable integration options
- Consider a platform that offers certified and ready-to-use APIs and connectors. This predefined versatility simplifies integration with leading cloud services (AWS, Azure IoT) as well as specialized platforms such as Cumulocity, Splunk, SAS Viya and other data analytics tools.
3. Ease of deployment and maintenance
Reducing downtime during the initial deployment or implementation of extensions is a critical success factor for the long-term manageability of digital industry project evolutions.
- Look for solutions that allow quick commissioning and easy configuration
- Your team should be able to implement pilot projects or PoCs in days or weeks, not months.
4. Adaptable and standardizable data models
- Standardization of machine data models ensures consistency when data moves across the enterprise, whether it is an MES, a quality management system or a data science platform.
This consistency also enables interoperability between different applications and future data-driven projects.
5. Safety and Compliance
- As data flows beyond the production floor to edge and cloud applications, robust security measures and compliance with industry standards become mandatory.
Make sure your platform can meet current safety requirements and regulations, and they will surely evolve in a restrictive direction, for different regions and sectors.
A real case for an industrial vehicle manufacturer. Monitoring machine utilization and production performance.
PHASE 1 - The initial goal was to obtain a solution to track and measure production performance, gaining an up-to-date view regarding:
- OEE
- Availability
- Cycle time
- Scraps
They chose Alleantia's IoT software for its broad support of protocols and certified API connectors, seamlessly connecting data from decades-old CNC machines to a modern MES in a matter of weeks.
PHASE 2 - Several months later, the manufacturer decided to extend its data analysis capabilities.
The goal was to delve deeper into monitoring the execution of the machines' actual work schedules to identify causes of performance slowdowns.
This was achieved by using a powerful business intelligence and reporting platform to implement massive data analysis.
The Alleantia solution already had a standard machine data model available in an accessible format. This made it immediate to implement the BI platform connection, without costly redesigns or complex data migrations.
Alleantia has added edge computing capabilities to implement real-time data aggregation and correlation to support highly detailed analysis models.
Within two months, the analysis system was completed providing engineers with additional data and tools to take action on continuous improvement of operational efficiency.
And so...what to do?
Adopting an open, cross-platform IoT platform today means breaking free from the constraints of a single vendor and gaining maximum operational flexibility.
The company can thus integrate-and replace-analytical tools of different kinds at any time, choosing the most effective solution for new business objectives on a case-by-case basis.
This freedom to experiment accelerates innovation, reduces the risks of obsolescence, and enables the rapid exploitation of emerging technologies, ensuring a truly “future-proof” digital transformation path.
Ultimately, only those who build their ecosystem on open standards can continue to grow, adapt and remain competitive in an ever-changing market.
Choosing an industrial IoT solution that avoids vertical silos and supports cross-platform connectivity is essential for any modern industry.
Are you ready to explore a super scalable approach to industrial digitization?
Take a look at the integration capabilities of the Alleantia platform, and find out if your current application platforms are supported.
Contact us for more information and learn how Alleantia's IoT platform can accelerate your digital transformation journey, reduce integration costs, and open up new possibilities.
Related articles
Data Integration - What are the benefits?