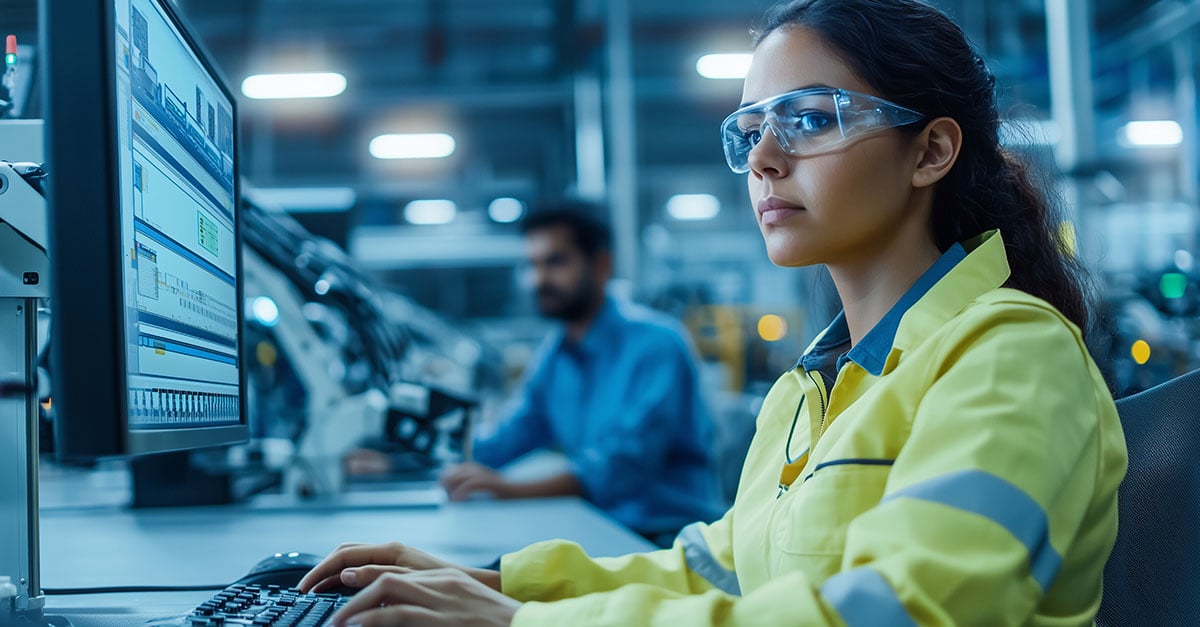
Il digital twin e l’importanza dei dati
Il concetto di Industry 4.0 e il digital twin sono le nuove frontiere della concezione, sviluppo, manutenzione e gestione degli asset nei processi di produzione aziendali.
Il concetto di digital twin nasce diversi anni fa ma, solo ultimamente, e con l’avvento dell’IoT, si è avuto lo sviluppo che ne conosciamo tutti noi.
Digital Twin cos'è?
Il gemello digitale non è solo un progetto o una rappresentazione grafica semplificata di una macchina o di un sistema più o meno articolato e complesso: è l’oggetto reale in pieno esercizio delle sue funzioni che si attua grazie alla sensoristica a bordo.
Tutto questo non è solo una rappresentazione virtuale: il gemello digitale è sì una rappresentazione virtuale, ma con l’aggiunta di quella parte fisica nel suo ciclo di vita che lo rende funzionale al proprio scopo. Utilizza dati in tempo reale e altre fonti per migliorare la sua “rappresentazione” e rispecchiare la realtà che rappresenta.
La realtà del Digital Twin
Occorre considerare il potenziale disruptive di questa articolata procedura tecnologica, anche alla luce della sua rilevante possibilità di aggregare molteplici dispositivi IoT, garantendo pertanto dati di analisi e sistemi predittivi accurati per sistemi complessi ed articolati.
Chiaramente, l’insieme dei dati raccolti, consentono interventi in tempo reale sull’esercizio efficace ed efficiente di un asset, ove necessario, ma anche di poter gestire i processi di progettazione ed ottimizzazione del prodotto, con una consapevolezza che non ha avuto eguali nei periodi passati.
I principali vantaggi dell'adozione del Digital Twin
L’adozione di un digital twin consente un monitoraggio da remoto real-time di un asset in esercizio, connette sistemi anche complessi e al contempo promuove la tracciabilità, rende più accurata la formulazione di ipotesi comportamentali con l’analisi predittiva e consente la risoluzione da remoto di criticità ravvisate in apparecchiatura lontane. Abilita, infine, lo sviluppo e l’affinamento di nuovi modelli di business in chiave sostenibilità.
Grazie all’ausilio dei KPI, i criteri progettuali divengono sempre più sofisticati e rispondenti alla specificità delle esigenze, consentendo al prodotto di rispondere sempre più accuratamente al proprio scopo ed in alcuni casi anche del suo utilizzo personalizzato, di resistere adeguatamente con garanzie di obiettivi di performance alle sollecitazioni e di poter meglio rispondere all’ambiente di esercizio.
Tutte le definizioni di Digital Twin sono accomunate da tre elementi distintivi:
- Il Digital Twin è una replica virtuale di un elemento fisico potenziale o attuale (Physical Twin), come un asset, un processo, una persona, un luogo, un sistema o un device;
- La replica virtuale contiene gli elementi chiave e le dinamiche di come un elemento fisico opera ed evolve nel corso del suo ciclo di vita, definiti in base agli obiettivi del Digital Twin;
- Viene stabilita una connessione tra elemento fisico e replica virtuale tramite lo scambio dati real-time, raccolti da sensori sull’elemento fisico e inviati alla replica virtuale.
L’importanza dei dati e il loro ruolo
Si indentificano quattro livelli di raccolta dei dati, che si differenziano in base alla frequenza con cui il sistema mette a disposizione i dati raccolti, garantendone la qualità.
Di seguito i principali risultati:
- Batch: le analisi vengono svolte in modalità batch, è previsto dunque un aggiornamento del sistema che prende in carico i dati raccolti a intervalli regolari predefiniti (56%). Classico è l’esempio di quei sistemi che elaborano i dati raccolti nella giornata lavorativa durante la notte successiva;
- Near Real Time: un sistema che svolge le analisi con una frequenza d’aggiornamento che si riduce a intervalli di tempo solitamente identificati da ore o minuti (33%);
- Real Time: il sistema è alimentato con dati raccolti in tempo reale che possono essere interrogati quando se ne ha l’esigenza (8%);
- Streaming: vi è un flusso continuo di raccolta dei dati che devono essere analizzati con continuità. Il sistema è dunque capace di supportare il flusso costante dei dati. Questa capacità viene richiesta nel momento in cui è presente un insieme di sensori che identificano valori che variano in maniera continua nel tempo (3%).
Quali sono le competenze richieste per l'implementazione di un Digital Twin?
La rivoluzione in atto portata da Industria 4.0, e da tutte le sue tecnologie, sta cambiando, e rapidamente, specie nelle imprese più innovative, professioni e competenze; e non sempre la “formazione” delle risorse umane è in linea con le novità in arrivo. In un quadro del genere formazione e apprendimento (possibilmente permanente) rappresentano una scelta obbligata per lavoratori e imprese.
In questo scenario, diventa dunque sempre più importante un approccio al life long learning, essenziale a tutti i livelli attraverso investimenti formativi aziendali e personali.
Alle competenze tecniche sempre più sarà fondamentale avere e sviluppare soft skill: conoscenze informatiche e dei sistemi informativi, capacità di sapersi muovere in spazi cyber fisici, capacità di progettazione e di lavoro per obiettivi, ma anche spirito imprenditoriale ed apertura al cambiamento, così come capacità decisionale, autonomia organizzativa e problem solving.
In conclusione, i principali vantaggi Industrial IoT derivanti dal digital twin sono che:
Un’impresa manifatturiera digitalizzata e tecnologicamente all’avanguardia è produttivamente flessibile, capace di rispondere rapidamente ai cambiamenti del mercato e di gestirli efficacemente. Tra gli obiettivi tangibili raggiungibili la qualità dei prodotti finiti, l’estensione della rete distributiva, la diversificazione dell’offerta, l’innovazione di prodotto.
Il risultato finale è un miglior posizionamento competitivo dell’azienda rispetto ai concorrenti che, tradotto in termini materiali, implica migliori risultati economici che rendono percorribili scenari di ulteriore crescita.
La digitalizzazione è uno strumento potente di competitività per le imprese, la cui adozione richiede tuttavia la disponibilità di competenze e di un’organizzazione in grado di massimizzarne l’efficacia.