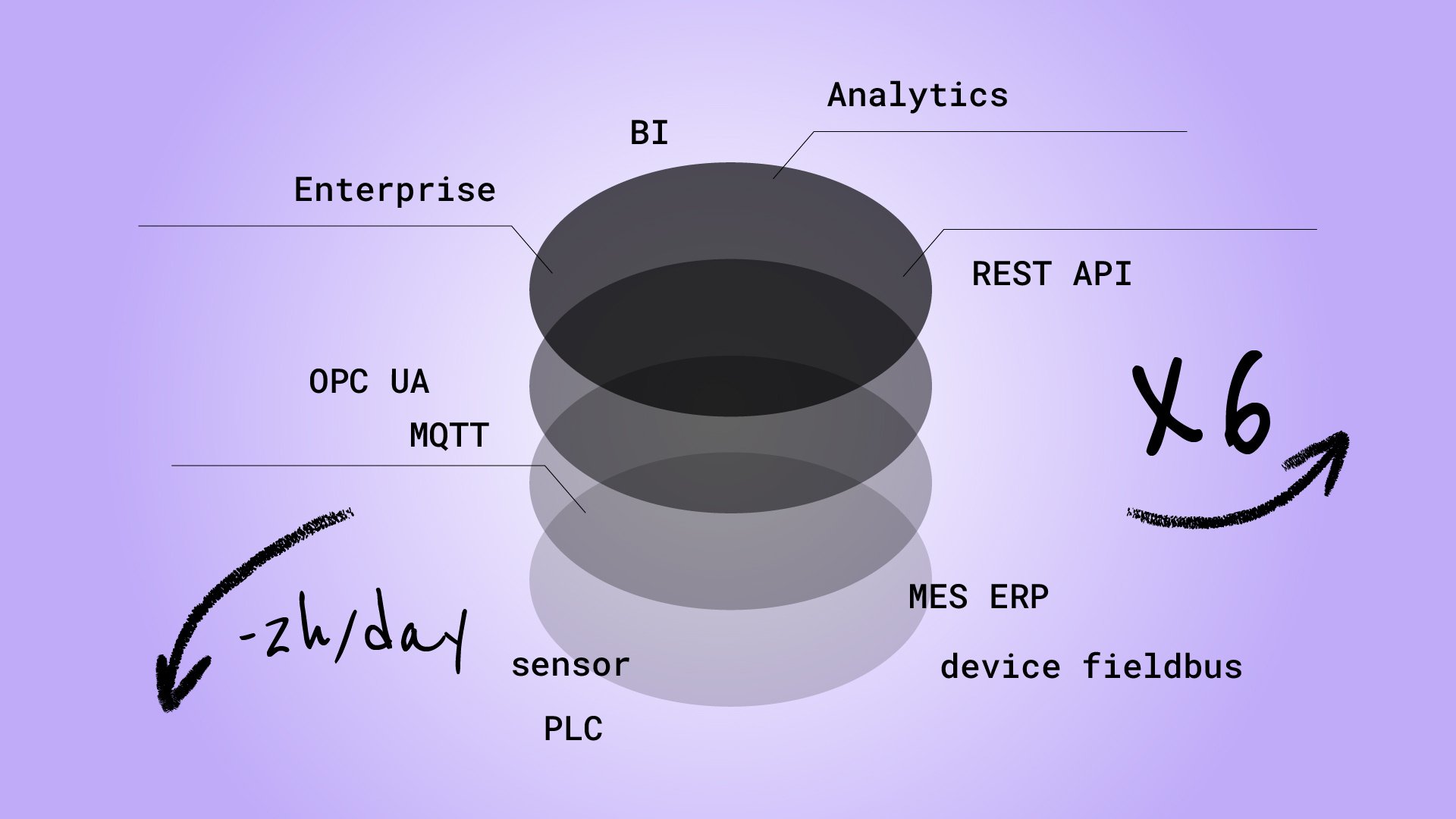
Digital Twin: manufacturing excellence through virtual replication
The data driven digital twin is the new frontier of asset design, development, maintenance, and management in corporate production processes.
The digital twin was born several years ago, but only with the advent of IoT has been the development that we know today.
What is Twin Model?
The digital twin is not just a project or a simplified graphic representation of a machine or a more or less articulated and complex system: it is the object in the exercise of its functions thanks to the onboard sensors.
All this is not just a virtual representation: the digital twin is a virtual representation, but the addition of that physical part in its life cycle that makes it functional to its purpose. It uses real-time data and other sources to enhance its "representation" and reflect the reality it represents.
The reality of Digital Twin
It is necessary to consider the disruptive potential of this technological tool, which can aggregate multiple IoT devices, thus guaranteeing accurate analysis data and predictive systems for complex and articulated systems.
The data collected allows real-time interventions on the effective and efficient operation of an asset, and manage the processes of design and optimization of the product, with an awareness that has had no equal in past periods.
Key benefits of adopting Digital Twin
The adoption of a digital twin allows real-time remote monitoring of an asset in operation, connects even complex systems, and at the same time promotes traceability, making the formulation of behavioral hypotheses more accurate with predictive analysis.
Finally, it enables the development and refinement of new business models based on sustainability.
With KPI (read more here), from real-time monitoring of the digital twin in operation, allowing the product to respond more accurately to its purpose and in some cases even to its custom use, to resist adequately with guarantees of performance objectives to stress and to be able to better respond to the operating environment.
All Digital Twin definitions share three distinctive elements:
- The Digital Twin is a virtual replica of a potential or actual physical elements (Physical Twin), such as an asset, process, person, place, system, or device;
- The virtual replica contains the key elements and dynamics of how a physical operates and evolves over its lifecycle, defined according to the Digital Twin objectives;
- A connection is created between the physical and the virtual by exchanging real-time data collected by sensors on the physical element and sent to the virtual replica.
The importance of data and its role
Four levels of data collection are identified, which differ according to the frequency with which the system makes the collected data available, guaranteeing its quality.
Below are the key findings:
- Batch: there is an update at regular predefined intervals (56%). A classic example is those systems that process data collected during the working day overnight;
- Near Real-Time: a system that performs analysis with an update identified by hours or minutes (33%);
- Real-Time: the system is fed with data collected in real-time and queried when the need arises (8%);
- Streaming: there is a continuous flow of data collection, analyzed continuously. Therefore, the system is capable of supporting the constant flow of data. It is required when sensors vary over time (3%).
What skills are required to implement a Digital Twin?
The revolution brought by Industry 4.0, and all its technologies, is changing jobs and skills; and the "training" of human resources is not always in line with the incoming changes. In such a framework, training and learning (possibly lifelong) represent a compulsory choice for workers and companies.
In this scenario, a lifelong learning approach becomes important, essential at all levels through corporate and personal training investments.
In addition to technical skills, it will be increasingly important to have and develop soft skills: knowledge of IT and information systems, ability to move in cyber-physical spaces, ability to plan and work towards objectives, but also entrepreneurial spirit and openness to change, as well as decision-making skills, organizational autonomy and problem-solving.
In conclusion, the main Industrial IoT benefits from the digital twin are:
A digitized company is flexible and able to respond quickly to market changes and manage them effectively. The achievable goals are the quality of finished products, the extension of the distribution network, the diversification of the offer, and product innovation.
The result is a better competitive positioning of the company concerning its competitors, translated into material terms, implies better economic results that make growth scenarios feasible.
Download Alleantia ISC Software, and test, COMPLETELY FREE, the digital twin software!